
CALL US : 01803 449877
How Powder Coating Works
At South West Powder Coating, we provide a full start-to-finish service. The first step is to take whatever is being painted and prepare the material for powder. This may only require a light sanding and degreasing, but for refurbishment and for steel with a lot of work, Shot Blasting is an incredibly efficient and effective method of removing rust and surface contamination. Once the metal is prepared and checked for imperfections, we coat the metal in a fine, pain powder using Electrostatic Adhesion. Once coated, this layer is baked in an oven at around 170 - 210°C, causing the paint to adhere to the surface. After a few final Quality Checks, the product is ready for delivery to you, or direct to your customer.
Preparing The Material for Powder
From the moment we start prepping the metal and wipe down material we look for any imperfections on the metal. Any excessive welding splat or large dents could potentially impact the final outcome of the products finish. The likes of welding splat can be removed, however excessive dents often require contact with the customer to let them know unless informed previously.
Once the material is checked for imperfections, the next step is to wipe down the material with a solution from pro clean, a degreaser designed to help reduce rust marks. After wiping down the material, the surface is cleared of any excess liquid using a clean microfiber cloth, followed by a once over with an air hose to get any dust or other particles that may be left behind. Our final step before powdering the item is to go over it with a blow torch. This process burns off any hairs left by the microfibers and makes the surfaces lovely and clean for powdering. Ensuring the material is properly prepared for powder is crucial for a good finish, as any imperfections can prevent adhesion of the paint, and worse still, any rust left untreated can continue to spread beneath the paint.

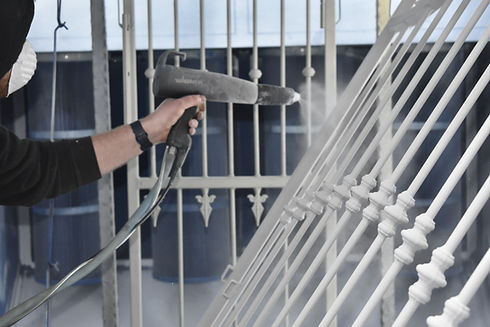
Powder Coating using Electrostatic Adhesion
Powder coating is a process that uses electrostatic air to coat a material, most commonly metal. A powder substance is blown through a gun causing the powder to become positively charged, a ground cable is attached to the item and this causes the powder to attract to it easily as it becomes negatively charged. The better the grounding the more efficiently the powder will cover and surround the part. Using this electrostatic method is incredibly efficient and creates an even finish by drawing in paint to exposed areas of metal. This electrostatic technique also minimises excess waste, as any excess powder that would otherwise disperse is instead drawn to the surface of the material. After the surface has been thoroughly inspected, the item is baked in a large, industrial oven to ensure the paint properly adheres to the material.
Quality Checks
Quality checks are crucial for any business, and for powder coating this is no different. Quality checks are performed at every step of the process, from the initial preparation of the material all the way through to checking the finished product post-bake. Once identified, problems are carefully resolved to prevent any potential complications or imperfections that may arise during later stages of the process and ensure a clean, even finish.

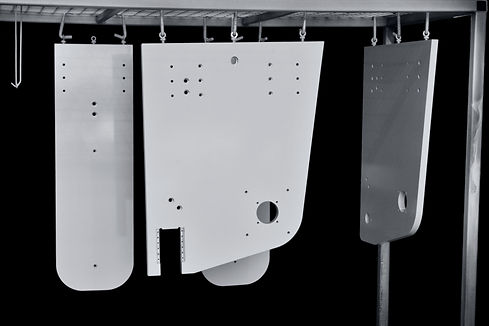
Types of Powder Coat Finishes
Powder coating comes in a few different forms. The simplest difference is found in the kind of surface finish. The most common finish is Gloss, offering a smooth, glossy, and slightly reflective finish surface. Gloss is typically has the best protection from the elements, as the bonding agents within it are stronger than those used in a matte finish. While gloss creates a reflective surface, matte finishes are flat and reflect little to no light. Matte finishes up close are a rougher, grainy texture, often regarded as more stylish and a "truer" colour. Between gloss and matte sits satin, with more neutral qualities across the board.
Using High Quality Powder
Our main powder supplier is Interpon, who have a fantastic reputation for supplying amazing service and quality.
Interpon Powder coatings are:
-
Solvent-free
-
Reduced risk of fire
-
Lead-free
-
Ease of waste disposal
-
No hazardous materials used during clean up
-
No Volatile Organic Compounds (VOC)
-
Contain no toxic heavy metals such as lead or chromium (VI)
-
No paint sludge from a spray booth
-
High Application Efficiency; recyclable, up to 99% usage, overspray can be reused
-
Improved productivity
-
One coat system, simple process
-
Can build high film thicknesses easily, up to 150 microns with one coat
-
No costly removal and reprocessing of solvents
-
Highly durable
-
Low carbon footprint
In conclusion, our Powder Coatings:
-
Give excellent performance
-
Meet the wide range of global coatings standards
-
Can offer significant cost benefits compared to liquid paints
-
Are safe and sustainable
